9 bolt to 9 inch
#1
Member
Thread Starter
Join Date: Jan 2004
Location: Augusta Georgia
Posts: 365
Likes: 0
Received 0 Likes
on
0 Posts
Car: 89 IROC
Engine: 95 350 LT1
Transmission: 4L60E
9 bolt to 9 inch
The 9 bolt in my car is shot. I pulled it out and measured it up, I happened to have a 28 spline 9 inch ford center section, so i stuck the 9 bolt axles in and measured it up, good news!, the pinion centerline was about 1/4 in away from the stock location! Tomorrow I'm going to make a jig so I can put the 9 bolt axle tubes on the 9 inch rear. Anyone here ever do a conversion like this?
#3
Moderator

Join Date: Jul 1999
Location: 51°N 114°W, 3500'
Posts: 17,165
Likes: 0
Received 136 Likes
on
114 Posts
Car: 87 IROC L98
Engine: 588 Alcohol BBC
Transmission: Powerglide
Axle/Gears: Ford 9"/31 spline spool/4.86
With some fabrication skills anything is possible. What are you going to do about the torque arm?
#4
Member
Thread Starter
Join Date: Jan 2004
Location: Augusta Georgia
Posts: 365
Likes: 0
Received 0 Likes
on
0 Posts
Car: 89 IROC
Engine: 95 350 LT1
Transmission: 4L60E
I thought about the axle tube size too. On most rear axles the torque from the differential is transmitted through the axle tubes into the suspension, but the beauty of our cars is all that torque is absorbed through the torque arm so axle strength isn't as critical. Because of this I doubt you would ever see a 3rd or 4th gen camaro spin the axle tube in the rear end housing. Braking torque is absorbed through the axle tube into the torque arm but that load is nothing compaired to how much torque the differential has to handle when your foot is in it.
I'll try to get some pictures posted.
I'll try to get some pictures posted.
#5
Member
Thread Starter
Join Date: Jan 2004
Location: Augusta Georgia
Posts: 365
Likes: 0
Received 0 Likes
on
0 Posts
Car: 89 IROC
Engine: 95 350 LT1
Transmission: 4L60E
about the torque arm- the 9 inch has 5 bolts that hold the pinion in, and it also has the nuts that hold the diff in the housing. I plan on making a bracket that will use some of these bolts/nuts to hold the torque arm. I've seen some 9 inch conversions where the torque arm bracket is mounted to the housing, this just puts an extra load on the housing.
#6
Moderator

Join Date: Jul 1999
Location: 51°N 114°W, 3500'
Posts: 17,165
Likes: 0
Received 136 Likes
on
114 Posts
Car: 87 IROC L98
Engine: 588 Alcohol BBC
Transmission: Powerglide
Axle/Gears: Ford 9"/31 spline spool/4.86
The pinion bearing housing and center section housing mounting bolts are not strong enough to hold the torque of the diff. They're only tiny 3/8" bolts.
#7
Member
Thread Starter
Join Date: Jan 2004
Location: Augusta Georgia
Posts: 365
Likes: 0
Received 0 Likes
on
0 Posts
Car: 89 IROC
Engine: 95 350 LT1
Transmission: 4L60E
if the bolts were too small then why would they use them to hold the rear together? I've seen the pinion carrier blown right out of ford rears, the bolts usually were not what broke, the carrier ears busted off.
My design will incorporate a pinion carrier reinforcement which will transmit most of the torque load directly to the pinion carrrier. the bolts that hold the diff in the housing will be under a shear load anyway. I could always drill those bolts out and use a 7/16 or 1/2 wheel stud in their place.
When you guys see it you'll understand.
My design will incorporate a pinion carrier reinforcement which will transmit most of the torque load directly to the pinion carrrier. the bolts that hold the diff in the housing will be under a shear load anyway. I could always drill those bolts out and use a 7/16 or 1/2 wheel stud in their place.
When you guys see it you'll understand.
Trending Topics
#8
I thought about doing exactly that till I hopelessly bent the axles in my 9bolt… basically just lop off the axle tubes, grab an axle assembly of your choice with a 28 spline carrier (9”, 8.8, mopar 8.75 are the top of my list, pretty much in reverse order) and weld the axle tubes so the length is right, you’ve already got “c-clip eliminators with the 9 bolt axle retention plates, you get brackets with the tubes… If you pick the right housing it’s just a simple matter of slipping the smaller 9botl tubes in and welding or at worst working out some sleeves to weld things together with.
With an 8.8 you’ve got some cast ribs in the housing that have mounting locations that were originally meant to hold dampening weights, or you could duplicate what some of the mustang retrofit TA’s use or something like the old SummersBrother’s f-body 12 bolt assembly.
FWIW, if you’re going to go off the pinion support I would strongly suggest using studs and making your plate a complete circle around the whole thing using all the bolts/studs to most evenly support the load. For that matter, I wouldn’t even consider this with some of the OEM housings because you’ll put a load on something that really was never designed to tolerate it and I wouldn’t be surprised if you got enough flex to damage the chunk or to mess with your pinion setting. Really, if it was me I would do this as a brace for the assembly, but not as a primary mount, which would really be strongest welded to the housing where you could distribute the load pretty much as much as you want.
With an 8.8 you’ve got some cast ribs in the housing that have mounting locations that were originally meant to hold dampening weights, or you could duplicate what some of the mustang retrofit TA’s use or something like the old SummersBrother’s f-body 12 bolt assembly.
FWIW, if you’re going to go off the pinion support I would strongly suggest using studs and making your plate a complete circle around the whole thing using all the bolts/studs to most evenly support the load. For that matter, I wouldn’t even consider this with some of the OEM housings because you’ll put a load on something that really was never designed to tolerate it and I wouldn’t be surprised if you got enough flex to damage the chunk or to mess with your pinion setting. Really, if it was me I would do this as a brace for the assembly, but not as a primary mount, which would really be strongest welded to the housing where you could distribute the load pretty much as much as you want.
#9
Member
Thread Starter
Join Date: Jan 2004
Location: Augusta Georgia
Posts: 365
Likes: 0
Received 0 Likes
on
0 Posts
Car: 89 IROC
Engine: 95 350 LT1
Transmission: 4L60E
did they make 28 spline 8.75 chrysler rears? I thought they were all 30 spline. I wasn't planning on mounting just off the pinion support, I was planning on using some carrier bolts too but that was yesterday. I already changed the design of my jig 3 times already.
I have these nice steel rings that I use to reinforce the pinion support, I'm too cheap to buy a daytona support. I'll probably use one of those rings
Did that summers bros 12 bolt actually work? Sandwiching a plate between the cover and housing didn't seem like such a good idea.
I know the strength of the 9 bolt axles is limited. A ford 9" is really overkill for what I'm doing but I have lots of 9" parts. If I had my way I would have gone with an 8" but parts are too scarce. I'm only planninig on running 3.25 gears, that should take the edge off the torque.
I have these nice steel rings that I use to reinforce the pinion support, I'm too cheap to buy a daytona support. I'll probably use one of those rings
Did that summers bros 12 bolt actually work? Sandwiching a plate between the cover and housing didn't seem like such a good idea.
I know the strength of the 9 bolt axles is limited. A ford 9" is really overkill for what I'm doing but I have lots of 9" parts. If I had my way I would have gone with an 8" but parts are too scarce. I'm only planninig on running 3.25 gears, that should take the edge off the torque.
#10
Originally posted by SERPENT99
did they make 28 spline 8.75 chrysler rears? I thought they were all 30 spline.
did they make 28 spline 8.75 chrysler rears? I thought they were all 30 spline.
I don’t know that any did OEM (I would be surprised if some didn’t, but oem’s do a lot of things that make you ask WTF were they thinking?), but dana 44 carrier side gears and spiders swap (you have to replace them in sets, AAMOF, the 8.75 ones don’t exist anymore so that is the only way to get new ones).
I have these nice steel rings that I use to reinforce the pinion support, I'm too cheap to buy a daytona support. I'll probably use one of those rings
Any pics of this? I have a Daytona on mine, but I’m still curious since I’m sure that I’ll be building up another chunk for it eventually.
Did that summers bros 12 bolt actually work? Sandwiching a plate between the cover and housing didn't seem like such a good idea.
Sandwitched plate… works fine. I’ve seen retrofit GNX setups done like that also. I suppose that if you wanted to start with an 8.5” 10 bolt (which would be plenty strong for 99% of cars) then you could use one of the aftermarket cast GNX knockoff covers with the ears for the TA mount cast into them.
I know the strength of the 9 bolt axles is limited. A ford 9" is really overkill for what I'm doing but I have lots of 9" parts. If I had my way I would have gone with an 8" but parts are too scarce. I'm only planninig on running 3.25 gears, that should take the edge off the torque.
#11
Member
Thread Starter
Join Date: Jan 2004
Location: Augusta Georgia
Posts: 365
Likes: 0
Received 0 Likes
on
0 Posts
Car: 89 IROC
Engine: 95 350 LT1
Transmission: 4L60E
Dude! What the hell did you do to that rear! Never saw anyting like that before. it must have been a bitch to get that axle out.
Anyway, here's my jeep rear with one of those rings. It's just a piece of 1/2 plate laser cut to fit over the pinion support.
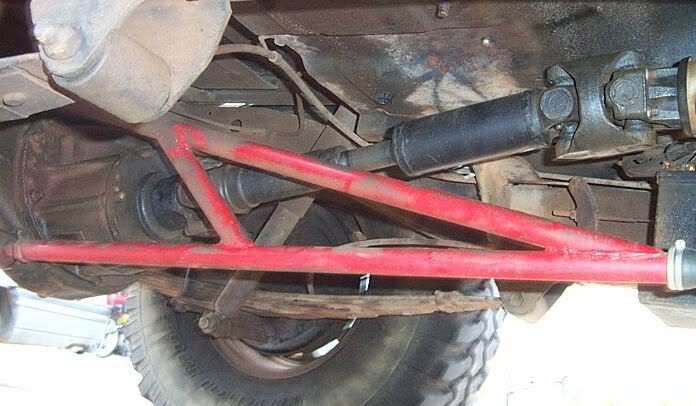
Here's what the jig looks like. I got lucky, the 9 bolt tubes fit right inside the ford tubes. The housing is really old, it's one with the smooth back cover that has 2 dimples and a fill plug.
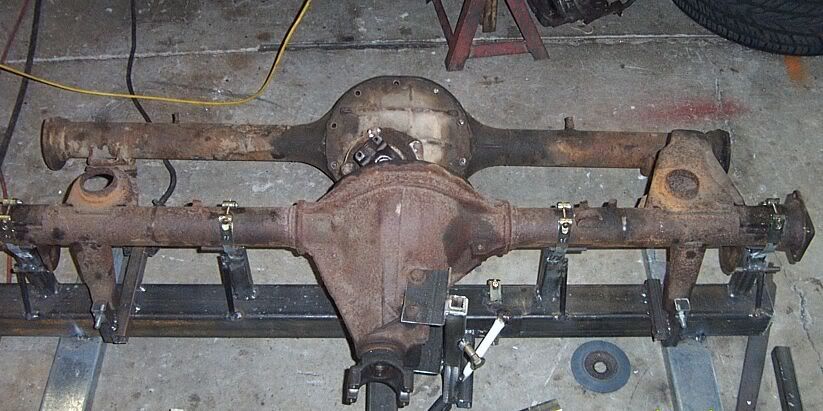
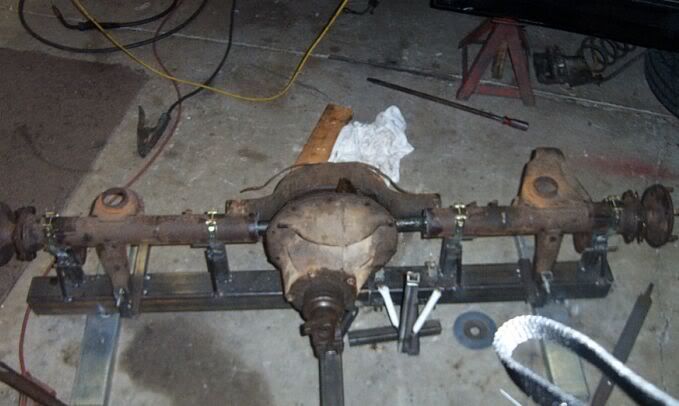
Anyway, here's my jeep rear with one of those rings. It's just a piece of 1/2 plate laser cut to fit over the pinion support.
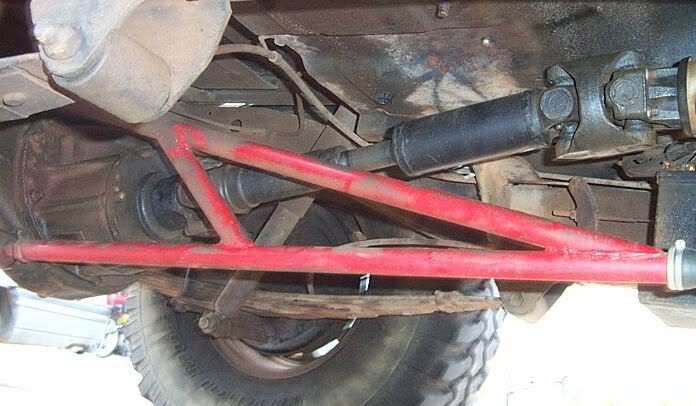
Here's what the jig looks like. I got lucky, the 9 bolt tubes fit right inside the ford tubes. The housing is really old, it's one with the smooth back cover that has 2 dimples and a fill plug.
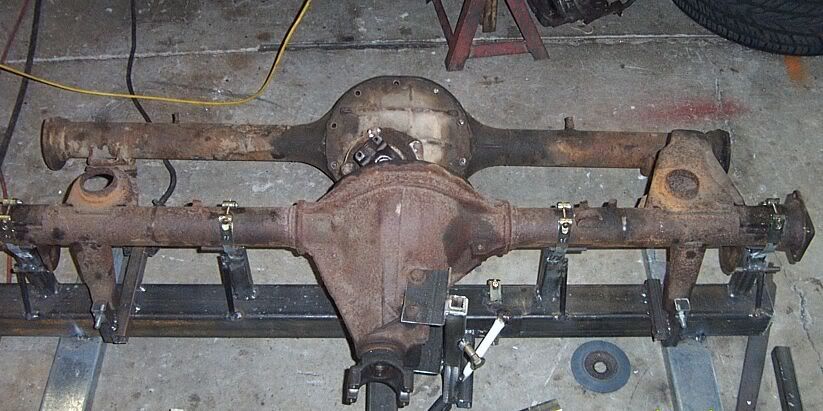
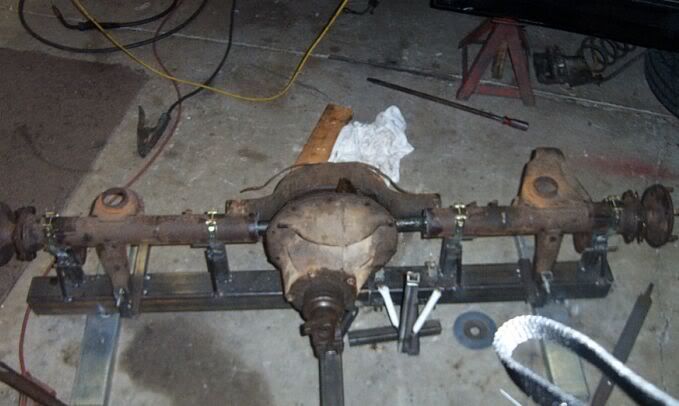
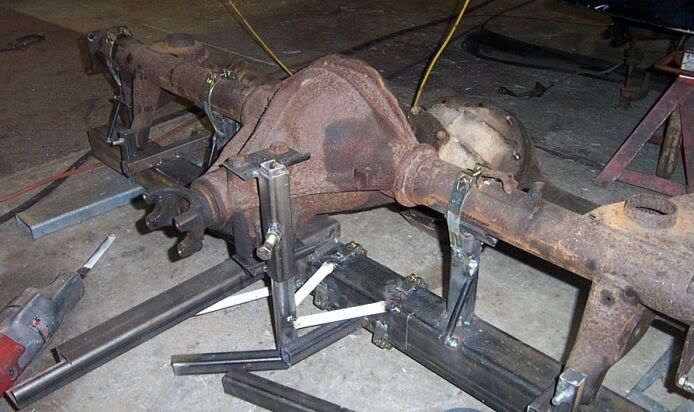
#13
Member
Thread Starter
Join Date: Jan 2004
Location: Augusta Georgia
Posts: 365
Likes: 0
Received 0 Likes
on
0 Posts
Car: 89 IROC
Engine: 95 350 LT1
Transmission: 4L60E
it's done. I checked it for straightness with a bar and some bushings I made and it came out good. I went off the housing with the torque arm bracket because it was easier and what 83 CTA said seemed to make sense. The pinion is about 1/2 inch off to the passenger side and the torque arm is about an inch and a half off to the driver side because of the fat pinion housing. May have to beat the floor a little. if the top torque arm mount bolt hits the floor I figure I'll cut a hole for clearance and I'll cut the hump out of the old 9 bolt cover and weld it over the hole. It's not a 9 second piece of work but considering what I plan on using the car for it should do just fine. Notice the welds on the axle tubes are offset top and bottom. This helps keep things straight, just do the hotizontal welds first and take your time on the rest, don't put too much heat into it at once
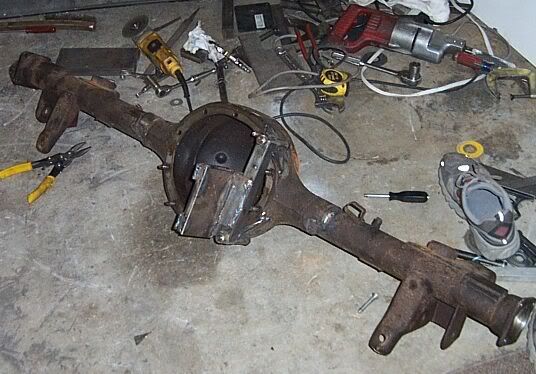
#16
Supreme Member

Join Date: Jan 2001
Location: Lincoln, Nebraska
Posts: 1,047
Likes: 0
Received 2 Likes
on
2 Posts
Car: 1988 Firebird, 2000 GTP
Engine: 327
Transmission: 700R4
Axle/Gears: 9" posi, 4.11
Sure beats what I'm doing. I got the crazy idea of cutting the brackets off the F-Body rear and weld them to the 9". So far I have got the spring perches off, but the control arm and shock mount are a whole different story. Those things make the project difficult. If anyone has tried this and had luck, let me know.. I've tried everything short of a plasma or oxy/acetyline torch.. really wish I had the plasma.. would have the job done in a minute or two.
Good job though.. congrats on it working out.
Good job though.. congrats on it working out.
#17
Member
Thread Starter
Join Date: Jan 2004
Location: Augusta Georgia
Posts: 365
Likes: 0
Received 0 Likes
on
0 Posts
Car: 89 IROC
Engine: 95 350 LT1
Transmission: 4L60E
All I need now is a drive shaft and some gear lube. The stock drive shaft would probably work with one of those conversion U-joints but the slip yoke would be a little further out of the trans than I would like it to be. The diff I'm using is open as in one legged but at least I'll be free of that horrible howl that 9 bolt made. The 9 bolt was 2.77 and the nine inch is 2.75. This is temporary until I get some parts to make a nice posi with maybe 3.25 or 3.50 gears. I do a lot of highway driving so I like those ratio's. When i have it apart for the new gears and posi I'm also going to put new axle bearings in and maybe polish the axles to make them a little stronger. I'm glad the housing I used had a fill plug in the back of it, the torque arm bracket I made completely blocked the fill plug in the carrier. I left the springs out and jacked it all the way up to the bump stops and it clears everthing! I thought for sure I'd be hammering the floor somewhere. Tomorrow I'm going to the junkyard, GM used the same U-joint that the ford rear uses on some of their earlier cars, spicer size 1310. If I can find a drive shaft 42 1/8 long center to center then I'm all set. The trans yoke for the 4L60E is the same size as a lot of the older cars too so If my luck holds out I may find something that will bolt right in. Now I just need to find a posi unit somewhere.
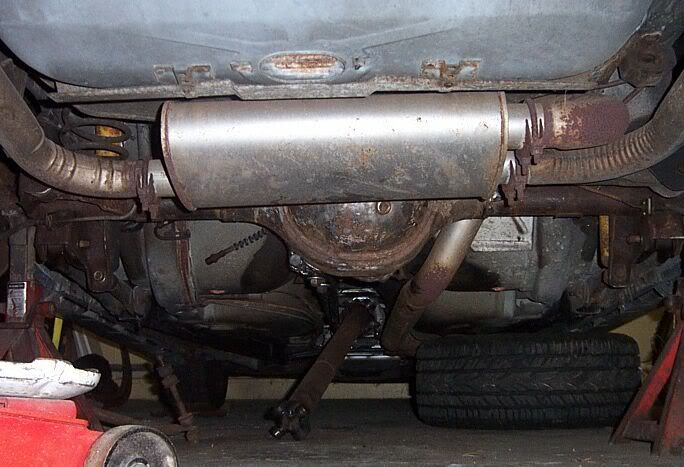
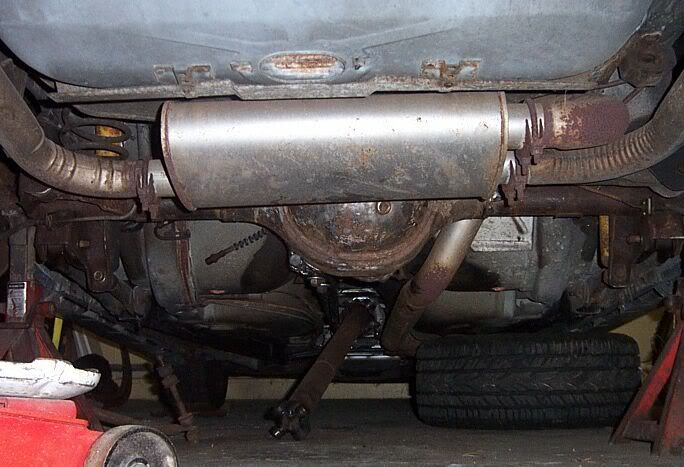
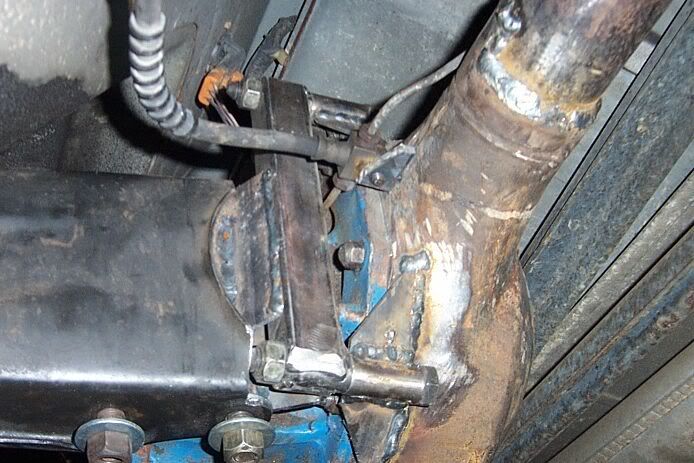
#18
Member
Join Date: Jan 2004
Location: Chagrin Falls, Ohio
Posts: 391
Likes: 0
Received 0 Likes
on
0 Posts
This is a very interesting thread.
My first question is how did you get from this picture:
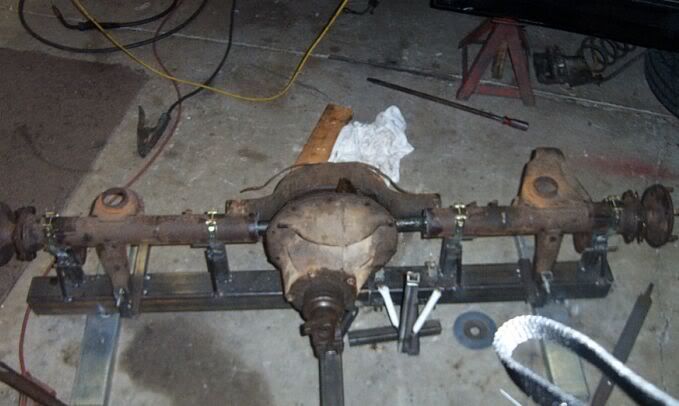
to having the middle of the 9inch housing in between the tubes? I would assume you'd have to take atleast one of the tubes off the jig, but then you'd lose its exact place.
Did your tubes slide right into the ford housing and you welded it up or is there more to it than that?
What if you were using a 10 bolt as the donor rear end, how do you think you might be able to retain the axles?
and lastly, i assume that if you wanted 31 spline axles you'd have to get them custom made by moser or the likes.
Thanks ahead of time for any input you can give
My first question is how did you get from this picture:
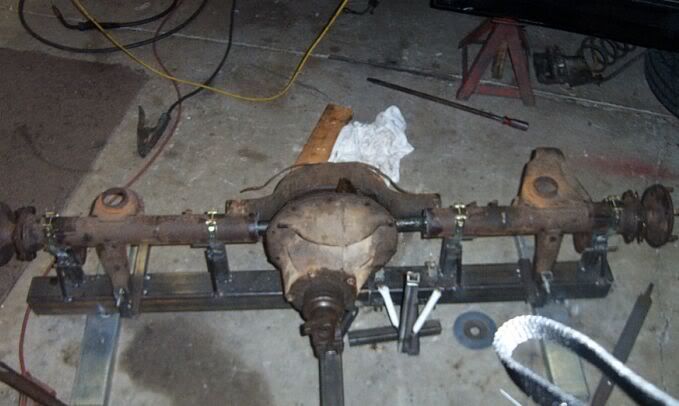
to having the middle of the 9inch housing in between the tubes? I would assume you'd have to take atleast one of the tubes off the jig, but then you'd lose its exact place.
Did your tubes slide right into the ford housing and you welded it up or is there more to it than that?
What if you were using a 10 bolt as the donor rear end, how do you think you might be able to retain the axles?
and lastly, i assume that if you wanted 31 spline axles you'd have to get them custom made by moser or the likes.
Thanks ahead of time for any input you can give
#19
To use a normal 10 bolt housing you’ll need to use someone’s c-clip eliminator ends (Moser sells weld on billet ones that use a big ford/olds bearing that are pretty nice), or a center section like an ford 8.8 that has previsions for c-clips.
Moser will supposedly do axles in the spline count you want with any bearing seat and hub that you want (as long as it’s larger then the spline count). I ordered my moser rear with 3rd gen hub sizes (they usually come with the later 4th gen size since it’s smaller and fits everything), 3rd gen length, the ford/olds rear bearing assembly with spacers/ends to fit the 4th gen brackets.
Moser will supposedly do axles in the spline count you want with any bearing seat and hub that you want (as long as it’s larger then the spline count). I ordered my moser rear with 3rd gen hub sizes (they usually come with the later 4th gen size since it’s smaller and fits everything), 3rd gen length, the ford/olds rear bearing assembly with spacers/ends to fit the 4th gen brackets.
#20
Member
Thread Starter
Join Date: Jan 2004
Location: Augusta Georgia
Posts: 365
Likes: 0
Received 0 Likes
on
0 Posts
Car: 89 IROC
Engine: 95 350 LT1
Transmission: 4L60E
I removed one of the tubes to get the 9 inch center in. The tube was located with 2 v blocks with clamps, it also had a bracket on the shock mount and a stop that touched the control arm mount so it went back in pretty much where it was. The 9 bolt tubes slid inside the 9 inch housing, this made things really easy. I put it all together loose, then before I welded anything I slid the 9 inch housing/ differential left and right to where the end of the axle hit the spider gear cross shaft, I put it in the middle of those points. Then I set the pinion angle off the piece of tubing that sticks out under the pinion and welded it all together.
I found a driveshaft and yoke in the junkyard that used the same 1310 series ujoints that the ford rear used. I took it for a ride and it was smooth as silk. Total cost was about $50 for the driveshaft, some gear lube and new U bolts for the yoke. it was so nice to be rid of that howl that the 9 bolt made.
83 CTA is right, they'll make any axle any way you want, but the spline can only as big as the hole in the wheel bearing you plan on using.
I got lucky on this whole project. The splines matched, the pinion location changed very little, the tubes slid inside one another and both GM and Ford used 1310 series ujoints which meant finding a driveshaft in the junkyard was possible.
The hardest part was making the torque arm bracket.
I found a driveshaft and yoke in the junkyard that used the same 1310 series ujoints that the ford rear used. I took it for a ride and it was smooth as silk. Total cost was about $50 for the driveshaft, some gear lube and new U bolts for the yoke. it was so nice to be rid of that howl that the 9 bolt made.
83 CTA is right, they'll make any axle any way you want, but the spline can only as big as the hole in the wheel bearing you plan on using.
I got lucky on this whole project. The splines matched, the pinion location changed very little, the tubes slid inside one another and both GM and Ford used 1310 series ujoints which meant finding a driveshaft in the junkyard was possible.
The hardest part was making the torque arm bracket.
#22
Member
Thread Starter
Join Date: Jan 2004
Location: Augusta Georgia
Posts: 365
Likes: 0
Received 0 Likes
on
0 Posts
Car: 89 IROC
Engine: 95 350 LT1
Transmission: 4L60E
they're special high pressure hose clamps, it's all I had. Regular hose clamps would have worked just as good.
#23
Supreme Member

Join Date: Jan 2001
Location: Lincoln, Nebraska
Posts: 1,047
Likes: 0
Received 2 Likes
on
2 Posts
Car: 1988 Firebird, 2000 GTP
Engine: 327
Transmission: 700R4
Axle/Gears: 9" posi, 4.11
LOL.. well I figured out how to get the brackets off. For anyone who cares.
Cut the welds down as far as you can.. reach over, pick up sledge hammer, hit bracket!
I know it's not the best method, but I was getting tired of working on this for a week. Nothing bent by using careful hits, but I was able to fracture the welds and get the brackets off.
I should have both sides off by the weekend and ready to start setting them up on the 9"
You have inspired me to get this done. I was lucky and picked up a complete 28spline 9" with all brake hardware and a 4.11 posi carrier
$200
Cut the welds down as far as you can.. reach over, pick up sledge hammer, hit bracket!
I know it's not the best method, but I was getting tired of working on this for a week. Nothing bent by using careful hits, but I was able to fracture the welds and get the brackets off.
I should have both sides off by the weekend and ready to start setting them up on the 9"
You have inspired me to get this done. I was lucky and picked up a complete 28spline 9" with all brake hardware and a 4.11 posi carrier

#24
Senior Member
Join Date: Feb 2005
Location: Kirkland Washington
Posts: 661
Likes: 0
Received 0 Likes
on
0 Posts
Car: 84 Camaro. 90 integra
Engine: LG4, 1.6 (402hp)
Transmission: 700r4, JDM ITR w/ kaaz LSD
Whats the Overall differance in the rear-ends? my dumb question.
#25
Member
Thread Starter
Join Date: Jan 2004
Location: Augusta Georgia
Posts: 365
Likes: 0
Received 0 Likes
on
0 Posts
Car: 89 IROC
Engine: 95 350 LT1
Transmission: 4L60E
the 9 inch is stronger, easier to work on and easier to find parts for. Also, I can set up another carrier with some lower gears and swap it out in an hour to go drag racing and swap it back when I'm done..
#26
so your in alt...hmmm thats not far from here...how much would you charge to weld the center section up with no TA mount? just the tubes and center section? i bring the parts..
thanks chris..

thanks chris..
#27
Member
Thread Starter
Join Date: Jan 2004
Location: Augusta Georgia
Posts: 365
Likes: 0
Received 0 Likes
on
0 Posts
Car: 89 IROC
Engine: 95 350 LT1
Transmission: 4L60E
I'll weld it up for you. Email me off list serpent99@charter.net and we'll make a deal. I'll trade work for car parts or computer parts and cash is always welcome.
#28
I finally have some real time to reply here…
First, that fill plug, is that orginal or did someone just drill/tap that in? do you have a drain plug?
I don’t think that either axle on that thing is ever coming out. I couldn’t budge it with a real axle puller (with a 15 or 20lb slide hammer assembly). As far as I can tell I’ve actually twisted the axle so it’s corkscrewed. Like I said, till that happened something like your approach was going to be the way I was going to go.
Yea, that is one seriously old 9”, with the narrower webbing where the axle tubes fit in and the smooth back… Like I said earlier, with the right housings it should be a slide in deal, that way you can use the welded stubs inside the axle as alignment points…
heh, could be but you’d have to upgrade just about everthing inside it and make a stronger TA mount…
Do you have a better picture of this? I can’t see what you’re talking about. The more traditional approach is to jig it up, tack it as best you can and weld a serious bead the whole way then check it for straightness and heat shrink the side that it’s bent away from if it’s bent at all…
The moser one does to, but it doesn’t come with a fill plug…
Actually, no, and if you ended up using a ford DS with a 1310 end it will look like it fits but it’s actually a bit off. GM used a Saginaw S44 and there is actually a proper crossover from an S44 to a 1310.
First, that fill plug, is that orginal or did someone just drill/tap that in? do you have a drain plug?
Originally posted by SERPENT99
Dude! What the hell did you do to that rear! Never saw anyting like that before. it must have been a bitch to get that axle out.
Dude! What the hell did you do to that rear! Never saw anyting like that before. it must have been a bitch to get that axle out.
I don’t think that either axle on that thing is ever coming out. I couldn’t budge it with a real axle puller (with a 15 or 20lb slide hammer assembly). As far as I can tell I’ve actually twisted the axle so it’s corkscrewed. Like I said, till that happened something like your approach was going to be the way I was going to go.
Here's what the jig looks like. I got lucky, the 9 bolt tubes fit right inside the ford tubes. The housing is really old, it's one with the smooth back cover that has 2 dimples and a fill plug.
Yea, that is one seriously old 9”, with the narrower webbing where the axle tubes fit in and the smooth back… Like I said earlier, with the right housings it should be a slide in deal, that way you can use the welded stubs inside the axle as alignment points…
It's not a 9 second piece of work but considering what I plan on using the car for it should do just fine.
heh, could be but you’d have to upgrade just about everthing inside it and make a stronger TA mount…
Notice the welds on the axle tubes are offset top and bottom. This helps keep things straight, just do the hotizontal welds first and take your time on the rest, don't put too much heat into it at once
Do you have a better picture of this? I can’t see what you’re talking about. The more traditional approach is to jig it up, tack it as best you can and weld a serious bead the whole way then check it for straightness and heat shrink the side that it’s bent away from if it’s bent at all…
Originally posted by SERPENT99
L'm glad the housing I used had a fill plug in the back of it, the torque arm bracket I made completely blocked the fill plug in the carrier.
L'm glad the housing I used had a fill plug in the back of it, the torque arm bracket I made completely blocked the fill plug in the carrier.
The moser one does to, but it doesn’t come with a fill plug…
GM used the same U-joint that the ford rear uses on some of their earlier cars, spicer size 1310. If I can find a drive shaft 42 1/8 long center to center then I'm all set.
Actually, no, and if you ended up using a ford DS with a 1310 end it will look like it fits but it’s actually a bit off. GM used a Saginaw S44 and there is actually a proper crossover from an S44 to a 1310.
#29
Member
Join Date: Aug 2002
Location: Blaine WA
Posts: 162
Likes: 0
Received 0 Likes
on
0 Posts
Car: 84 Z28
Engine: 355/460hp
Transmission: glide\ford 9"
thought I might include my home made 9"
pic didn't work so disregard.
pic didn't work so disregard.
Last edited by 84406; 04-02-2005 at 10:32 AM.
#30
Member
Thread Starter
Join Date: Jan 2004
Location: Augusta Georgia
Posts: 365
Likes: 0
Received 0 Likes
on
0 Posts
Car: 89 IROC
Engine: 95 350 LT1
Transmission: 4L60E
email me the pic I'll post it. serpent99@charter.net
to answer some of 83 CTA's questions-
The housing came from the factory with the fill plug. No drain plug though, I'll probably put one in when I change out the center. It will get a 3.23 posi soon- this is a highway car.
About the weld- I'll find a picture. What I did was cut halfway vertically through the tube, then make a horizontal cut for about an inch then cut the other half. When I join the tubes I weld the horizontal part first and it helps keep things from walking around. Also- you would be surprised on how much warpage you can see just by looking down the tubes with the diff removed. After the hosing is done I use the heat and shrink like you mentioned but sometimes the housings are so bad you have to cut the end off and weld it on straight. I have a bar and bushings to check the ends.
On the jeep I v cut the housing before I welded the tubes in, like the step cut, this increases the weld area makes the junction between the 2 tunes stronger.
About the U joints, I think what you said may explain something. Sometimes I have trouble fitting the clips in, sometimes it's loose. I have a whole box of clips of different thickness so I just use a matched set of thicker or thinner clips. I've had this car up to 142 mph and had no vibration at all. You really notice the dips in the road at that speed and you also notice how bad the stock brakes are.
to answer some of 83 CTA's questions-
The housing came from the factory with the fill plug. No drain plug though, I'll probably put one in when I change out the center. It will get a 3.23 posi soon- this is a highway car.
About the weld- I'll find a picture. What I did was cut halfway vertically through the tube, then make a horizontal cut for about an inch then cut the other half. When I join the tubes I weld the horizontal part first and it helps keep things from walking around. Also- you would be surprised on how much warpage you can see just by looking down the tubes with the diff removed. After the hosing is done I use the heat and shrink like you mentioned but sometimes the housings are so bad you have to cut the end off and weld it on straight. I have a bar and bushings to check the ends.
On the jeep I v cut the housing before I welded the tubes in, like the step cut, this increases the weld area makes the junction between the 2 tunes stronger.
About the U joints, I think what you said may explain something. Sometimes I have trouble fitting the clips in, sometimes it's loose. I have a whole box of clips of different thickness so I just use a matched set of thicker or thinner clips. I've had this car up to 142 mph and had no vibration at all. You really notice the dips in the road at that speed and you also notice how bad the stock brakes are.
#31
Member
Join Date: Aug 2002
Location: Blaine WA
Posts: 162
Likes: 0
Received 0 Likes
on
0 Posts
Car: 84 Z28
Engine: 355/460hp
Transmission: glide\ford 9"
Serpent99, thanks for the offer of the pic post. I think I sent the large file by mistake and it got turfed. Wasn't good shot anyway. For interest I made my 9" out of a mid 80's pickup rear and only had to narrow one side. If you are interested I could PM you on how I did it all. If there is other interest I could start a new thread as I don't want to hijack yours.
TZFBird, you probably have the mounting tabs off by now but I found it went quite quick as the ford tubes are much larger and therefore the tabs need quite a bit of trimming, so being prefect on the cut off in not that important.
TZFBird, you probably have the mounting tabs off by now but I found it went quite quick as the ford tubes are much larger and therefore the tabs need quite a bit of trimming, so being prefect on the cut off in not that important.
#32
Member
Join Date: Feb 2005
Location: michigan
Posts: 130
Likes: 0
Received 0 Likes
on
0 Posts
Car: 85 z28
Engine: 327
Transmission: th350
Axle/Gears: ford 9in 4:56 to 1
Originally posted by 84406
For interest I made my 9" out of a mid 80's pickup rear and only had to narrow one side. If you are interested I could PM you on how I did it all.
For interest I made my 9" out of a mid 80's pickup rear and only had to narrow one side. If you are interested I could PM you on how I did it all.
#33
Member
Join Date: Aug 2002
Location: Blaine WA
Posts: 162
Likes: 0
Received 0 Likes
on
0 Posts
Car: 84 Z28
Engine: 355/460hp
Transmission: glide\ford 9"
ZDRAG28
I tired to send you the file but it was too long to be taken so if you could give me your email address I will send it along.
I tired to send you the file but it was too long to be taken so if you could give me your email address I will send it along.
#35
Member
Thread Starter
Join Date: Jan 2004
Location: Augusta Georgia
Posts: 365
Likes: 0
Received 0 Likes
on
0 Posts
Car: 89 IROC
Engine: 95 350 LT1
Transmission: 4L60E
well, finally got a new center section. 3.25 gears and a ford posi with a billet side cover. The difference between the 2.75 and the 3.25 was noticeable. Also put a transgo 4L60E-HD2 shift kit in, it took me 3 tries to get it right
Man, this car is so much fun to drive. I'm taking a road trip next week from Augusta to Long Island. No wife, no kids, just me, the car, the Who, Jimi Hendrix, Pink Floyd, some Nine Inch Nails and a new pair of sunglasses. Time to enjoy all the work I put into this thing.

Man, this car is so much fun to drive. I'm taking a road trip next week from Augusta to Long Island. No wife, no kids, just me, the car, the Who, Jimi Hendrix, Pink Floyd, some Nine Inch Nails and a new pair of sunglasses. Time to enjoy all the work I put into this thing.
#36
Supreme Member

damn chris, nice work as always. I've considering doing something similar once I graduate and have more time on my hands. going to be building a trans crossmember and torque arm later this week.
#38
Member
Thread Starter
Join Date: Jan 2004
Location: Augusta Georgia
Posts: 365
Likes: 0
Received 0 Likes
on
0 Posts
Car: 89 IROC
Engine: 95 350 LT1
Transmission: 4L60E
the jig is pretty much self explanatory. The only thing I would do is move the inner supports away from the diff housing. The old housing was used as a jig to make the jig. Look over the pictures and if you have any questions let me know. Plans aren't really needed.
Thread
Thread Starter
Forum
Replies
Last Post
Hotrodboba400
Firebirds for Sale
3
12-10-2019 07:07 PM
UltRoadWarrior9
Transmissions and Drivetrain
3
09-02-2015 08:24 PM